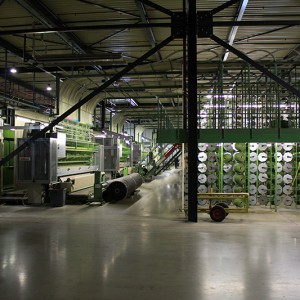
How do we manufacture artificial grass?
When it comes to the quality of artificial grass manufacturing, great differences can be found. For instance, most types of artificial turf are made with single backing (the fabric on the bottom), but all Royal Grass® manufactured artificial grass products are made with double backing. This makes the artificial grass firmer and easier to install. It also gives the grass more back support and protects it against shrinking and expanding.
You want another example? Sure.
Our thread (i.e. the grass itself) doesn’t contain any heavy metals. Why is that something we like to point out? Well, many other brands make artificial grass with colour pigments that contain small concentrations of heavy metals. We all know about the strict rules for plastic toys, but when it comes to artificial grass these do not apply. Weird, don’t you think? We agree. We want your children to be able to play safely on your artificial lawn, so we decided to use only fibres that are 100% clean and safe.
Does the quality of the material have an influence on the way artificial grass is produced?
No, not really. The manufacturing process is pretty much uniform, regardless of artificial grass quality. Let us explain the production of artificial grass in five steps.
Step 1 – Tufting
The manufacturing process requires two resources: fibre and backing. The fibres are delivered on large spools, and the backing on rolls of more than 4 meters in the width. First of all, we have to put these two together. This happens with the so-called tufting machine.
The fibres are put through tubes that are hanging on top of the machine and into needles. These needles will stitch the fibres from above into the backing. Subsequently, the thread is pulled back by a hook thus creating a loop. We call this process tufting.
Sounds familiar? That’s probably because it is virtually the same process as on a sewing machine. The main difference, however, is that the thread disappears in the fabric and the grass needs to stand up straight in the backing.
Step 2 – Coating
The fibres have now been put in the backing, but they haven’t been fixed yet. If you’d grab one of the fibres at the bottom of the backing, it will be pulled out straight away. To solve this, the bottom side will be provided with a protective layer. This layer is a coating of glue to make sure the fibres will stick to the backing.
We can apply this coating with two different methods. In case of most machines, the artificial grass enters the machine with the backing face up and the coating will then be pulled over the backing.
The other method is the one we at Royal Grass® use. We insert the artificial grass with the backing face down. The coating is then ‘licked’ to the bottom side resulting in a more equal and smooth result.
Does the thickness of the coating matter?
It sure does. Here we can also find a difference between artificial grass of good quality and that of lower quality. A thinner coating layer means a lower cost price. But with a thin coating layer, the fibres will be fixed in a less solid way into the backing, so they can easily become loose when the artificial lawn is installed.
I guess you understand why we are using a thicker coating. Right?
Step 3 – Drying
The difference between quality artificial grass and mediocre artificial grass also lies in the way the coating is dried.
Normally, artificial grass is put straight into the oven to dry. We, on the other hand, use a different drying method. We first put the artificial grass in an infrared booth. Inside the grass is given a good ‘wallop’. You can say we give the grass a good scare. By doing so the coating will already lose much of its moisture.
The main advantage of this process is that the oven can be set to a lower temperature.
Why does this matter?
Well, you’ll probably know that if something is left to dry for a longer period of time, the result will be better, more beautiful and stronger. This applies to paint, your hair, a cake in the oven, glue… everything really. And so also to artificial grass.
Of course, we understand that you can set the oven to a higher temperature so the coating will dry more quickly. The grass can be put around the spool faster and more meters of artificial grass can be produced per hour. Thus if you’re only thinking about costs, it’d make sense to choose this option. However, if you’ve got quality on your mind we say: nah, rather not.
Step 4 – Perforating
Artificial grass needs to be perforated because otherwise rainwater can’t escape leaving you with puddles of mud on your artificial lawn.
So even though this may seem like a small step in the process, it is highly important.
Are there any differences in this? No. That being said, it is definitely an advantage that our backing consists of a double layer. This makes it more solid than most other backings. With every hole you make in the material, you lessen its integrity. But: the thicker the material, the less impact this has.
Royal Grass® artificial grass is almost ready…
Step 5 – Rolling
Do you know what is probably the most underrated and perhaps also the trickiest part of the production process of artificial grass? Rolling it up. Or dragging, as they say here in our factory.
The grass is 4 meters wide when it is dragged onto cardboard spools. The difficulty lies in making sure the tension that comes onto the grass is exactly – and we mean exactly – the same across the entire width of the spool.
So what happens if the tension isn’t the same everywhere? Well, in places with less tension, the grass will ripple. The grass will have room to manoeuvre and to expand leading to pieces that are no longer suitable for use.
Try manually rolling up a piece of carpet. You will notice it will be tight in the middle, but somewhat loose around the edges. So when you unroll the carpet after a week or so, those edges will be curly.
And that is something we most certainly don’t want. What we do want is a uniform quality, across the entire width of the spool.
So that’s it…
The artificial grass manufacturing process has been completed and the artificial grass is ready. It is wrapped in plastic to protect it against outside influences, and then stored in the warehouse. It is ready for global transport.
This is what a artificial grass manufacturer does, in a nutshell. A very big nutshell indeed.
If you have any questions, please do not hesitate to give us a call. As a premium manufacturer artificial grass, we would be happy to explain the choices we have made for the production process.